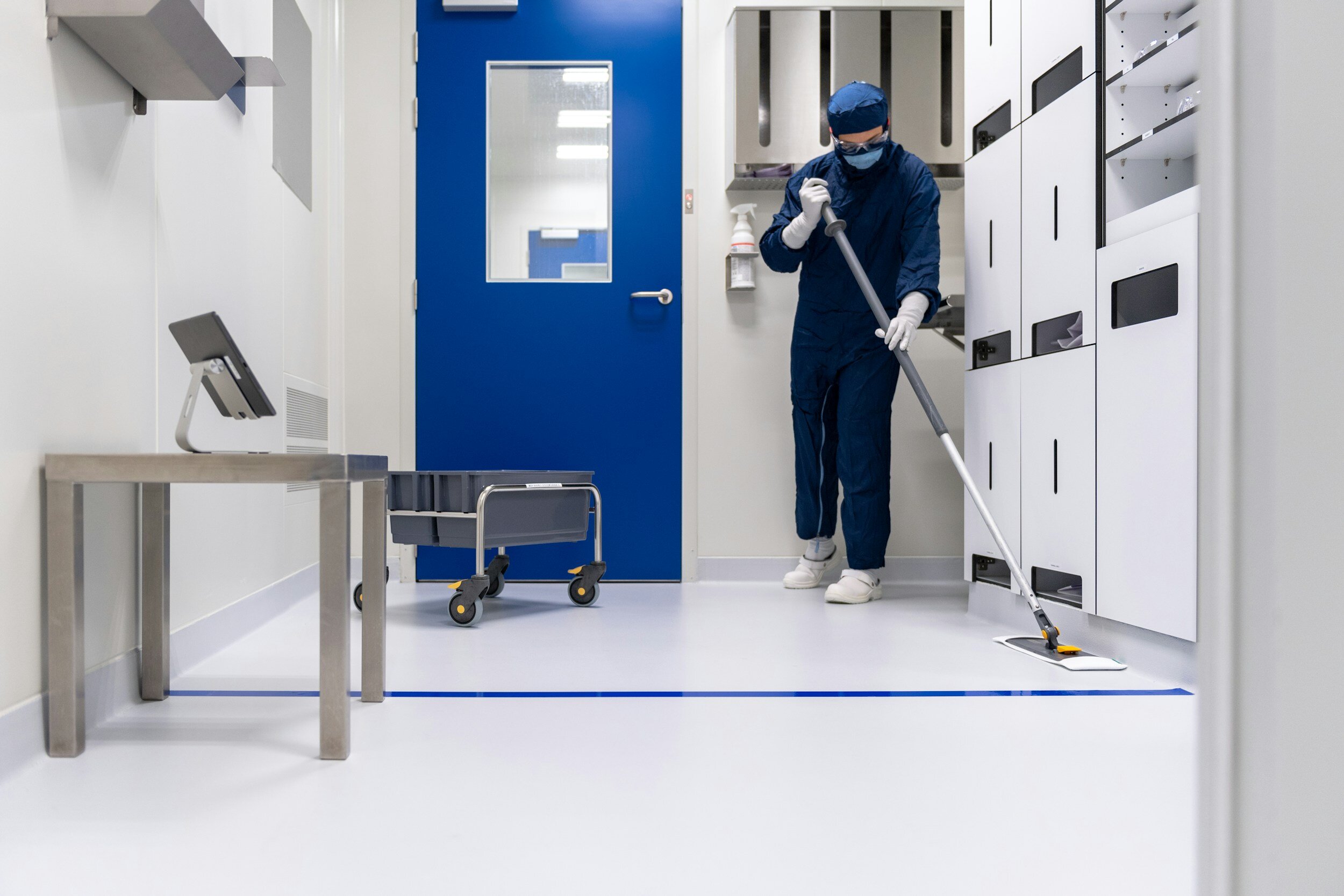
Cleanroom - pharmaceutical - Medical
We recognize that particulates in cleanrooms, pharmaceutical, and medical are deposited onto surfaces such as floors, walls, work surfaces and machinery, and that these particulates may cause increases in manufacturing reject rates or cross contamination. Viable and non-viable particulate loads can also lead to product contamination safety concerns for end users. To reduce these risks, it is imperative that customers design, implement, and maintain an effective cleanroom cleaning program. Our team can play an important role in this cleaning program by providing trained technicians to perform specialized cleaning services on a daily, weekly, or monthly basis with specifications as determined by the customer.
UNDERSTANDING CLEANROOM PROCESSES
Cleanrooms vary widely in use. Manufacturing cleanrooms don’t have the same functions or standards as pharmaceutical or laboratory cleanrooms. Depending on your industry, your cleanroom will have a specific layout, ISO rating, and cleanliness standard. Therefore, its cleaning schedule and procedure will also differ.
Cleanrooms with higher ISO ratings must be kept at much higher levels of sanitation to reduce the chance of interference of minute particles and contaminants. Conversely, cleanrooms with lower class ratings may be less threatened by certain contaminants or smaller particle sizes, but they still require regular cleaning to maintain standards and efficiency.
Contamination Prevention Protocols
The best way to keep your cleanroom clean is to follow proper sanitation techniques before entering a cleanroom. These include washing and drying hands completely, using sterile and not powdered gloves, following the proper gowning procedure for your ISO class, and ensuring all employees can access garments and tools that fit them.
In a perfect world, we would prevent contamination by introducing zero contaminants into your cleanroom environment. Of course, this is virtually impossible, so regular cleaning and maintenance of your cleanroom and its systems is critical.
Use High-Quality Products Approved for Cleaning Cleanrooms
Cleaning products that are improperly sterilized or unsuitable for cleanroom use can cause contamination. You should use deionized and distilled water for mopping and wiping surfaces and use only cleanroom-specified cleaning agents. All chemicals and solvents for cleaning must be neutral, non-ionic, and non-foaming to avoid buildup on surfaces over time. High ISO class cleanrooms (ISO level 5-7) often require disinfectants to be sterilized before use, further protecting the cleanroom from any contaminants.
Never use scrubs or rags that could shed or corrode surfaces. Instead, only use woven polyester that is specified for cleanroom use. Employ a mopping system that separates dirty and clean water and will not scratch or contaminate the floor or walls. Follow a mopping protocol that efficiently cleans floors without spreading dirty water over cleaned areas.
It’s also a good practice to bring all materials that will be needed — such as brooms, mops, and cleaning agents — into the cleanroom before beginning to clean. This way, once the process is complete, you only need to exit once, reducing the possibility of contamination.
Medical
In a medical facility, there is no room for error. From booking appointments to blood draws to preparing for surgery, you are driven by quality and safety. Your environmental services provider must be as well.
When servicing any facility, Our first priority is to provide the highest level of decontamination through advanced and effective surface cleaning and specialized cross-contamination prevention methods. Our staff is carefully trained to keep healthcare facilities safe, sanitary, and healthy for your patients and your staff.
Anti-bacterial cleaning methods differ from those applied in an ordinary work or home environment. Our technicians follow a strict cleaning and sanitization regimen in health care units, medical offices and all health related facilities. Our cleaning products are EPA approved and safe for all common and critical care areas. Customized cleaning plans are specially devised for each location to ensure safety as well as effectiveness.